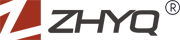
1. Ammonia synthesis link
1.1 Raw gas purity monitoring: In the process of ammonia synthesis, the purity of the raw gas (nitrogen and hydrogen) is crucial to the reaction efficiency and product quality. Inline process refractometer can indirectly monitor the impurity content by detecting the refractive index change of the impurity gas in the raw gas. For example, if the raw gas contains water vapor or other hydrocarbon impurities, its refractive index will be different from that of pure nitrogen and hydrogen. In this way, the quality problems of the raw gas can be discovered in time to ensure that the purity of the raw gas entering the synthesis tower meets the requirements, thereby improving the reaction efficiency of ammonia synthesis.
1.2. Reaction process monitoring: The ammonia synthesis reaction is a reversible reaction. The concentration change of the gas components during the reaction will affect the reaction equilibrium. Inline process refractometer can be installed on the reaction pipeline to monitor the refractive index change of the reaction system in real time. This change can reflect the concentration change of the reaction gas. According to the change of the refractive index, the operator can adjust the reaction conditions, such as temperature, pressure and gas flow rate, in time to ensure that the reaction proceeds in the direction of ammonia generation and improve the synthesis rate of ammonia.
2. Urea production process
2.1 Raw material concentration control: In the urea production process, the main raw materials are ammonia and carbon dioxide. Inline process refractometer can accurately measure the concentration of ammonia solution to ensure that ammonia participates in the reaction at an appropriate concentration. For carbon dioxide raw materials, although it is a gas, it will be dissolved in solution in some production processes, and the refractometer can also monitor its concentration. For example, in the carbon dioxide stripping process, accurate control of the concentration of carbon dioxide solution plays a key role in the reaction rate and product quality of urea synthesis.
2.2 Reaction progress monitoring: Urea synthesis reaction is a complex chemical reaction. The concentration change of each substance during the reaction will cause the refractive index of the reaction system to change. By monitoring the change of refractive index through the Inline process refractometer, the progress of the reaction can be understood in real time. When the refractive index reaches a certain stable value, it indicates that the reaction is close to completion or has reached equilibrium. This helps operators accurately control the reaction time and avoid over- or under-reaction, thereby ensuring the quality and production efficiency of urea products.
3. Product quality testing link
3.1 Nitrogen fertilizer purity detection: For the nitrogen fertilizer products produced (such as urea, ammonium nitrogen fertilizer, etc.), the Inline process refractometer can quickly detect their purity. The purity of nitrogen fertilizer directly affects its fertilizer efficiency. By measuring the refractive index of the product with a refractometer and comparing it with the refractive index of nitrogen fertilizer with standard purity, it can be determined whether the product meets the quality standard. For example, high-purity urea products have a specific refractive index range. If the measured value exceeds this range, it may indicate that the product contains impurities and requires further analysis and treatment.
3.2 Moisture content monitoring (indirect): In nitrogen fertilizer production, the moisture content of the product is an important quality indicator. Although the Inline process refractometer cannot directly measure the moisture content, the presence of water will affect the refractive index of the product. By establishing a relationship model between the refractive index and the moisture content, the moisture content in the nitrogen fertilizer product can be indirectly monitored. This is of great significance for controlling product quality, preventing product agglomeration, and ensuring the storage stability of fertilizers.
Your email address will not be published. Required fields are marked *