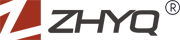
Inline refractometers play a very important role in detergent production.
1. Raw material quality control
1.1. The main component of detergent is surfactant, and it may also contain a variety of raw materials such as builders and thickeners. In the raw material acceptance link, inline refractometers can be used to detect the purity of raw materials. For example, for surfactants, surfactants of different purities have different refractive indices. Taking the commonly used sodium dodecylbenzene sulfonate as an example, its refractive index will change with the change of purity. By measuring its refractive index with inline refractometers and comparing it with the standard value, it is possible to quickly determine whether the raw materials meet the quality requirements and prevent raw materials with insufficient purity or impurities from entering the production line.
1.2. For some liquid raw materials, such as glycerol, refractometers can detect their concentration. Glycerol plays a role in moisturizing in detergents, and accurately controlling its concentration is important for the performance of detergents. If the glycerol concentration does not meet the requirements, it may affect the use of detergents.
2. Concentration control during production
2.1. Surfactant concentration control: Surfactants are the key components of detergents to play a decontamination role. In the process of detergent preparation, inline refractometers can monitor the concentration of surfactants in the mixed solution in real time. Since different types and concentrations of surfactant solutions have specific refractive index ranges, by continuously measuring the refractive index of the solution, production personnel can accurately control the amount of surfactant added. For example, when producing a certain dishwashing liquid, the concentration of the surfactant needs to be controlled within a certain range (such as 15% – 20%). Inline refractometers can adjust the feed rate of the surfactant in time to ensure the accuracy of its concentration based on the real-time measured refractive index and by comparing it with the pre-set concentration-refractive index curve.
2.2. Product consistency guarantee: The formula of detergent requires a relatively stable ratio of each ingredient to ensure the consistency of product quality. Inline refractometers help maintain this consistency. In large-scale production processes, environmental factors (such as temperature, humidity) or slight differences in equipment may affect the mixing effect of raw materials. By continuously monitoring the refractive index of the solution, the production control system can make timely adjustments to possible ingredient deviations. For example, if the refractive index of the detergent solution decreases for some reason, indicating that the concentration of a key ingredient may be reduced, the system can automatically increase the amount of the ingredient added to restore the product quality to the standard level.
3. Finished product quality inspection
Before the finished detergent is packaged, inline refractometers can perform the final quality control of the product. By testing the refractive index of the finished product, it can be verified whether the product meets the established quality standards. If the refractive index is outside the specified range, it may mean that the product’s ingredient ratio is incorrect or an abnormality has occurred during the production process. For example, it may be that too much or too little of a certain ingredient was added during the mixing process, or impurities were mixed in at the end of production. In this case, the problem product can be discovered in time to prevent unqualified products from entering the market.
Your email address will not be published. Required fields are marked *