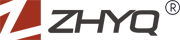
As an important tool for monitoring solution concentration, in-line process refractometer is widely used in many industries. In order to keep accuracy and stability of refractometer above certain standard, we need to strictly follow precautions from instruction booklet.
Surrounding environment and working conditions are two of the most important elements when installing in-line process refractometer. Avoid exposing in-line process refractometer to harsh conditions such as high temperature, humidity, corrosion, etc. Also, it is necessary to avoid installing the online concentration meter in a position directly affected by air flow or liquid wash, so as not to affect the accuracy of the measurement.
In-line process refractometer need to be pre-calibrated follow certain standard to ensure reliability of measuring result. The frequency of calibration should be determined according to the manufacturer’s recommendations and actual use. Regular maintenance is also essential to keep the sensor clean and sensitive to avoid performance degradation from long-term use.
In-line process refractometer is normally connected to a data acquisition system or data logger for real-time data collection and analysis purpose. However, in some case data is recorded from the field by test person due to some reasons. It requires frequent and accurate record to ensure anomalies can be discovered in time.
In-line process refractometer may be subject to abnormal conditions during monitoring process, such as concentration exceeding the predetermined range or equipment failure. Therefore, it is necessary to establish an emergency handling and alarm mechanism. Once the abnormal situation is detected, the alarm signal is sent in time, and the corresponding measures are taken.
For some industries such as chemical production and storage, in order to ensure the long-term stability and accuracy of the in-line process refractometer stay at certain standard, it is necessary to carry out periodic testing and recalibration on a regular basis. The performance of the in-line process refractometer can be verified by comparison with standard equipment or by zero-point calibration. Recalibrate or replace instrument when necessary.
Operators need to be pre-trained before operating and carry out maintenance to in-line process refractometer. This is to ensure they understand the basic principle of the instrument, operating procedures and safety precautions to minimise risks from work place and keep performance of the instrument.
Your email address will not be published. Required fields are marked *