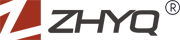
1. Raw material inspection process
1.1 Purity detection: The purity of various raw materials used in paint production, such as resins, solvents, additives, etc., has a direct impact on the performance of the paint. Inline process refractometers can quickly detect the refractive index of raw materials to determine whether their purity meets the requirements. For example, for solvents, the refractive index of solvents of different purities is different. By measuring the refractive index, raw materials with substandard purity can be found in time to prevent them from entering the production process and affecting the quality of the paint.
1.2 Concentration determination: Some raw materials may have concentration changes during procurement or storage. Inline process refractometers can accurately determine their concentration. Taking resin solution as an example, accurate measurement of its concentration helps to accurately mix the paint formula and ensure the stability of the paint performance.
2. Formula preparation process
2.1 Ratio control: The performance of the paint depends on the precise ratio of each component. Inline process refractometers can monitor the refractive index changes of each component during the mixing process in real time, so as to accurately control the amount of each raw material added and ensure the accuracy and consistency of the paint formula. For example, when mixing latex paint, the refractive index of the mixed components such as emulsion, pigment, and additives is monitored by a refractometer, and the proportion of each component is adjusted in time to achieve the best coating performance.
2.2 Compatibility detection: The compatibility between different raw materials is crucial to the stability and quality of the coating. Inline process refractometers can detect changes in the refractive index during the mixing process. If abnormal changes occur, it may mean that there are compatibility problems between the raw materials. It is necessary to adjust the formula or replace the raw materials in time to prevent the coating from having quality problems such as stratification and precipitation during use.
3. Reaction monitoring process
3.1 Polymerization reaction monitoring: In the production of paint, the synthesis of some resins needs to be achieved through polymerization reactions. Inline process refractometers can monitor the refractive index changes of the reaction system in real time, thereby reflecting the progress and degree of the polymerization reaction. As the polymerization reaction proceeds, the molecular weight and concentration of the polymer continue to increase, and the refractive index will change accordingly. By monitoring the refractive index, the reaction conditions, such as temperature and catalyst dosage, can be adjusted in time to ensure the smooth progress of the polymerization reaction and obtain a resin product with stable performance.
3.2 Cross-linking reaction control: For some coatings that require cross-linking reactions to improve performance, such as polyurethane coatings, inline process refractometers can be used to monitor the cross-linking reaction process. The cross-linking reaction will cause changes in the chemical structure and physical properties of the system, which will in turn cause changes in the refractive index. Through real-time monitoring of the refractometer, the degree of cross-linking reaction can be controlled so that the coating can obtain good hardness, wear resistance, corrosion resistance and other properties.
4. Dilution process
4.1 Diluent concentration control: Before the coating is used, it is usually necessary to dilute the coating according to the construction requirements. Inline process refractometers can monitor the concentration of the diluent in real time to ensure that the diluted coating reaches the appropriate construction viscosity and solid content. For example, during the coloring process of automotive topcoat, thinners are needed to clean the paint nozzles. ZHYQ’s inline process refractometers can effectively monitor the concentration of thinners and keep it at around Brix 1.00% to achieve a good spraying effect.
4.2 Determination of dilution ratio: Different coatings and construction conditions require different dilution ratios. Inline process refractometers can accurately determine the dilution ratio by measuring the change in the refractive index of the coating before and after dilution, ensuring good leveling, drying speed and coating quality of the coating during construction.
5. Quality control process
5.1 Finished product inspection: After the coating is produced, inline process refractometers can quickly detect the concentration, purity and other indicators of the finished coating to ensure that the product quality meets the standard requirements. For coatings of different types and uses, the refractive index has a certain range. The refractometer can be used to determine whether the product is qualified to prevent unqualified products from entering the market.
5.2 Stability evaluation: The stability of the coating is one of its important quality indicators. Long-term monitoring of the refractive index changes of coatings during storage and use by inline process refractometers can be used to evaluate the stability of coatings and predict their shelf life and service life. If the refractive index of coatings changes significantly during storage, it may mean that the coatings have deteriorated or delaminated, and timely measures must be taken.
Your email address will not be published. Required fields are marked *