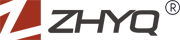
In the polymer chemical industry, inline process refractometers are an important detection and control instrument. The following are its specific applications:
1. Polymer synthesis process monitoring
1.1 Reaction process tracking: When synthesizing polymer materials such as rubber, plastics, and fibers, inline process refractometers can monitor the refractive index changes of the reaction solution in real time. Since the consumption of monomers, the generation of polymers, and the change in molecular weight during the reaction process will cause the change in the refractive index of the solution, by monitoring the refractive index, researchers and engineers can have a deep understanding of the progress and extent of the reaction, discover reaction abnormalities in a timely manner, and adjust reaction conditions such as temperature, pressure, and catalyst dosage, so as to ensure the performance and quality of the product and improve the stability and consistency of production. For example, when producing polyvinyl chloride (PVC), inline process refractometers can provide timely feedback on the conversion of monomers in the solution in order to adjust the reaction conditions and ensure the performance and quality of the product.
1.2 Molecular weight and distribution estimation: Although inline process refractometers cannot directly measure the molecular weight and distribution of polymers, there is a certain correlation between the refractive index and the molecular weight. By establishing a corresponding relationship model between refractive index and molecular weight, the molecular weight and distribution of polymers can be indirectly estimated. This is crucial for controlling the performance of polymers, because polymers with different molecular weights and distributions have different physical and mechanical properties, processing properties and application properties.
2. Quality control and product testing
2.1 Product concentration monitoring: For polymer solutions or melts, inline process refractometers can quickly and accurately measure their concentration. In the production process, strict control of product concentration is very important to ensure the consistency of product quality and performance. For example, when producing polyvinyl alcohol (PVA) fibers, the concentration of the spinning solution is an important parameter related to fiber quality, production process stability and production economic effects. Inline process refractometers can be directly installed in the production/discharge pipeline to monitor the Brix value of the liquid in the pipeline in real time, thereby ensuring that the concentration of the PVA spinning solution is stable within a suitable range, thereby ensuring the quality of the fiber and the smooth progress of production.
2.2 Impurity content detection: The presence of impurities will affect the performance and quality of polymer materials. Inline process refractometers can indirectly detect the content of impurities by monitoring the change in refractive index. When the solution contains impurities, its refractive index will change, and there is a difference with the refractive index of pure polymer solution. By comparing the refractive index with that of pure samples, the approximate content of impurities can be determined, so that timely measures can be taken to remove impurities or adjust the production process to ensure the purity and quality of the product.
3. Process optimization and cost control
3.1 Optimize reaction conditions: Real-time monitoring of refractive index changes during the reaction process by inline process refractometers can provide data support for process optimization. According to the trend of refractive index changes, the optimal reaction time, temperature, raw material ratio and other process parameters can be determined, thereby improving production efficiency, reducing energy consumption and raw material consumption, and achieving control and reduction of production costs.
3.2 Reduce scrap rate: Since inline process refractometers can detect abnormal conditions in the production process in a timely manner, such as reaction out of control, concentration deviation, etc., operators can quickly take corrective measures to avoid the generation of a large number of scraps, improve the qualified rate of products, and reduce production costs and resource waste.
4. Combined with other instruments to achieve automated control
4.1 Combined with PLC/DCS system: Inline process refractometers can be combined with automated control systems such as programmable logic controllers (PLC) or distributed control systems (DCS) to achieve automated monitoring and control of the production process. The refractometer transmits the real-time measured refractive index data to the PLC/DCS system, and the system automatically adjusts production parameters such as flow, temperature, stirring speed, etc. according to the preset control strategy, thereby achieving precise control of the polymer chemical production process, improving the automation level and intelligence level of production, reducing manual intervention, and improving production efficiency and product quality stability.
4.2 Combined with other analytical instruments: Inline process refractometers can also be combined with other analytical instruments such as chromatographs, mass spectrometers, infrared spectrometers, etc. to achieve more comprehensive and in-depth analysis and characterization of polymer materials. Through the collaborative work of multiple instruments, more information about the structure, composition, performance, etc. of polymer materials can be obtained, providing more powerful support for product development, quality control and process optimization.
Your email address will not be published. Required fields are marked *