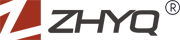
In safety management systems, pressure sensors implement side airbag control. Air compressor safety management systems are also areas where sensors are widely used. There are two options for controlling the side airbag of the air compressor: acceleration sensor and pressure sensor. Authoritative data shows that compared with acceleration sensors, pressure sensors are nearly three times faster than acceleration sensors in detecting the speed of side impacts, and the probability of malfunction is smaller. It is worth mentioning that miniaturized sensors use micro- Mechanical processing technology integrates and packages micron-level sensitive components, signal conditioners, and data processing devices on a single chip. Due to its small size, low price, and easy integration, it can improve the system test accuracy. For example, by integrating a micro pressure sensor and a micro temperature sensor to measure pressure and temperature at the same time, the pressure in the pressure measurement can be eliminated through on-chip calculations. Temperature effects. At present, many micro sensors are available.
Intelligent sensors are equipped with special computers, and their rapid development has improved the safety performance of air compressors to a higher level. With the development of microelectronics technology and micromachining technology, sensors are developing towards miniaturization, multi-function, and intelligence. Industry experts are therefore optimistic about the development prospects of air compressor sensors in China. They believe that the increase in the number of air compressors and the increase in sensors used on each air compressor determines that the capacity of China’s sensor market will continue to increase, and that China’s sensor market is entering a period of vigorous development.
Air compressors are essential equipment in various factories, road construction, mining and construction industries. They are mainly used to provide a continuous supply of compressed air with a certain pressure, such as supplying air to pneumatic valves and supplying gas that requires a certain pressure. Provide gas source for the process flow. There are many types of air compressors, such as screw air compressors, piston air compressors, centrifugal air compressors, scroll air compressors, etc. Screw air compressors have great market potential and are used in many industries. Be widely used. The air compressor uses a loading-unloading valve to control the air supply of the air compressor. Due to the working cycle of the air equipment or the difference in the production process, the air consumption fluctuates, sometimes causing the air compressor to be loaded frequently. uninstall. After the air compressor is unloaded, it still runs at power frequency, which not only wastes electric energy but also increases the mechanical wear and tear of the equipment. Moreover, loading is a sudden process, which will cause a greater impact on the equipment and the power grid. Therefore, the frequency conversion transformation of the air compressor can improve the starting and operation of the motor, reduce the mechanical wear of the equipment, and save electric energy within a certain range.
Taking a single screw air compressor as an example to illustrate the working principle of an air compressor, the working process of a screw air compressor is divided into four processes: suction, sealing and transportation, compression, and exhaust. When the screw rotates in the housing, the tooth grooves of the screw and the housing mesh with each other. Air is sucked in from the air inlet, and oil is also sucked in. Due to the rotation of the tooth groove meshing surface, the sucked oil and gas are sealed and transported to the exhaust port; during transportation During the process, the tooth groove meshing gap gradually becomes smaller, and the oil and gas are compressed; when the tooth groove meshing surface rotates to the exhaust port of the housing, the higher pressure oil and gas mixture is discharged from the body. The frequency converter can be used to change the exhaust volume by changing the screw rotor speed. When the air consumption changes, the frequency converter changes the speed to adjust the exhaust volume of the air compressor to achieve constant exhaust pressure and save energy. the goal of.
In the air compressor control system, the pressure sensor installed on the air outlet pipe at the rear end of the air compressor is used to control the pressure of the air compressor. When the air compressor starts, the loading solenoid valve is closed, the loading cylinder does not move, and the inverter drives the motor to run without load. After a period of time (can be set arbitrarily by the controller, here it is set to 10S), the loading solenoid valve opens. , the air compressor operates with load. When the air compressor starts running, if the back-end equipment uses a large amount of air and the compressed air pressure in the air storage tank and back-end pipeline does not reach the upper pressure limit, the controller will activate the loading valve, open the air inlet, and the motor will load operation, continuously producing compressed air to the rear end pipeline. If the back-end gas equipment stops using gas, the compressed gas pressure in the back-end pipeline and gas storage tank gradually increases. When the pressure upper limit setting value is reached, the pressure sensor sends an unloading signal, the loading solenoid valve stops working, and the air inlet The filter is closed and the motor runs without load.
When the air compressor continues to operate, the temperature of the compressor body will increase. When the temperature reaches a certain level, the system is set to 80°C (the controller can be set according to the application environment) and the fan starts running to reduce the operating temperature of the host. . After the fan has been running for a period of time, the temperature of the main unit drops and the fan stops running when it is lower than 75°C.
The pressure sensors commonly used on air compressors currently on the market include the pressure transmitter made of the SSI chip of the American SMI product and the American Honeywell MLH016BSB01B pressure sensor! Such products are mainly used in air compressors, water treatment equipment, industrial equipment, buildings, HVAC, petroleum, automobiles, etc., OEM factories.
Your email address will not be published. Required fields are marked *