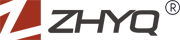
1. Pulping process
1.1. Black liquor concentration monitoring and control: Black liquor is the waste liquor from pulping and cooking in papermaking, and its concentration is crucial for subsequent treatment. Inline refractometers can measure the black liquor concentration in real time, such as accurately monitoring the feed black liquor concentration during the black liquor evaporation process to ensure that it is within the appropriate range. Too low a concentration will lead to low evaporation efficiency and increase the cost of steam use; too high a concentration will easily cause scaling and blockage.
1.2. Green liquor causticizing process control: In the causticizing process, when lime is added to green liquor to convert sodium carbonate into sodium hydroxide, inline refractometers can measure the green liquor concentration and help control the total alkali concentration in the green liquor within the appropriate range of 100-110 g/L, avoiding high viscosity and unfavorable sedimentation due to excessive green liquor concentration, thereby ensuring the smooth progress of the causticizing reaction and improving the quality and yield of sodium hydroxide.
2. Paper production process
2.1. Coating concentration monitoring: During paper coating, the concentration of coating affects the coating quality. Inline refractometers can monitor the concentration of coating in real time to ensure that it remains stable during the coating process, so that the paper can obtain a uniform coating and improve the quality indicators of the paper such as surface flatness, glossiness and printing adaptability.
2.2. Water repellent concentration control: When adding water repellent during the production process, inline refractometers can monitor the concentration of soluble solids in the water repellent in real time to ensure that the concentration of the water repellent is uniform, so that its efficacy can be stably exerted, giving the paper appropriate wet/dry strength and wet friction, and improving the stability and durability of the paper in a humid environment.
3. Quality control and optimization links
3.1. Improvement of product quality stability: Inline refractometers can monitor the concentration changes of various solutions in the production process in real time and continuously, so as to ensure that each batch of paper can meet the established quality standards and improve the stability and consistency of product quality.
3.2. Process optimization and cost control: By accumulating and analyzing the large amount of data measured by inline refractometers, engineers can deeply understand the relationship between various variables in the production process, find the bottlenecks in the production process, and then propose improvement measures to achieve process optimization and cost control. For example, parameters such as the amount of chemicals added, water temperature or pressure can be adjusted based on data to reduce energy consumption and increase production.
Your email address will not be published. Required fields are marked *