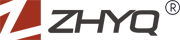
Introduction
Adhesives and sealants are used widely for joining , protecting and sealing systems in construction, manufacturing and maintenance.
This industry is facing challenges due to the limited raw materials (reserve of oil) and the negative impact of synthetic compounds on human health and environment. Key raw materials used for manufacturing adhesives are sourced from crude oil and petrochemicals. Volatile prices of these products have affected the profitability of participants in the recent past. Industry leaders are moving towards adoption of more advanced technologies such as automation, industrial internet of things (IIoT) and simulation techniques and are undertaking various strategic initiatives, such as extensive R & D activities for the sustainable production and cost-effective operations.
Industrial Applications & Market Insights of Adhesives and Sealants
Diverse sectors and industries use adhesives as part of its processes.
The adhesives & sealants market size is estimated to be USD 58.9 billion in 2019 and projected to reach USD 73.8 billion by 2024, at a CAGR of 4.6%, from 2019 to 2024 (projects by Markets and Markets). The increasing use of adhesives & sealants in various applications, such as paper & packaging, building & construction, woodworking, consumer/DIY, automotive & transportation, leather & footwear, assembly, and others is driving the growth of the adhesives & sealants market.
The automotive & transportation segment is expected to grow at the highest CAGR, in terms of value, during 2019-24, owing to an increase in the demand for lightweight, efficient, and eco-friendly cars. The rising demand for adhesives & sealants in fast-growing India, China, South Korea, Malaysia, Vietnam, Taiwan, Indonesia, among other countries in the region, is accelerating the growth of the adhesives & sealants market worldwide.
Application
A new range of high-strength industrial adhesives is now being used in the automotive field, and in other manufacturing operations, as a replacement for spot welding, mechanical fasteners, and other traditional joining methods. Adhesives offer several major advantages compared to conventional fastening techniques, including more uniform bond strength over a larger surface area, versus the localized strength points typically achieved with mechanical fastening. Adhesives are used to join surfaces, typically by changing their phase from liquid to solid. Sometimes this is triggered by a temperature change (hotmelt adhesives), in other cases the glue hardens at ambient conditions (contact adhesives) e.g. due to solvent evaporation or due to the humidity of the surrounding air.
Composition
Adhesives and sealants are complex formulations used to bind substrates or seal joints or gaps. They come in different forms but are commonly dispersions containing polymeric materials or curing agents, surfactants and solvents. Adhesives can be reactive or non-reactive. For reactive adhesives, adhesion can be induced by mixing two or more reactive components together, such as an epoxy resin and hardener, or can be induced by external stimuli such as UV radiation, heat or moisture. For non-reactive adhesives, adhesion is induced by physical stimuli such as pressure or solvent evaporation, for example. In the case of a sealant, the primary function is to seal joints or gaps and prevent moisture, solvents or gases from entering or escaping from a system or component, although many sealants can have multiple functions.
Most adhesives and sealants are composed of polymeric materials, or contain monomers or oligomers that form a cross-linked polymeric network following reaction. Consequently the molecular weight and molecular structure of these components are critical to material properties both before and after adhesion. Many adhesive and sealant formulations are two phase systems, which include emulsions containing dispersed polymer, or dispersed solids in the case of caulk. In both cases particle size and droplet size can be critical to product performance.
Anyone intending to use adhesives and sealants faces the formidable challenge of correct material selection as well as determining proper processes. The adhesive or sealant must flow onto the substrate surface and then change from a flowable liquid to a structural solid without creating harmful internal stresses in the joint. Many of the adhesive or sealant problems that evolve are not due to a poor choice of material or joint design but are directly related to faulty production techniques mostly lacking suitable process control.
Why viscosity measurement is important in preparing the formulations?
There are many types of adhesive and sealants to consider when setting up a manufacturing process. Careful consideration of viscosity helps choose the right material for both the design of product as well as the manufacturing process required to build it.
Modern adhesives are often a complex formulation of components that perform specialty functions. The formulation of raw materials into serviceable adhesive bonding and sealing systems is itself a broad field of technology. Adhesives and sealants can be produced in various forms: one- and two-part liquids, solvent based solutions, water-based emulsion, supported or unsupported film, preformed pellets or shaped extrusions, and numerous other forms. This variety of formulation possibilities and end-use forms are indicative of the advanced state of development of adhesives and sealants.
Viscosity (and Rheology) is one of the most important parameters in production and processing of adhesives. Further incoming material must be viscosity tested before use (e.g. in a dosing system). Various solvents, soluble agents, resinous powders, or inert fillers can be used to control the viscosity of the adhesive. Viscosity of adhesive systems may need to be increased or decreased depending on the application and operational environment.
Slow and critical processing requirements of some adhesives can be a major disadvantage particularly in high-volume production operations. If the adhesive has multiple components, the parts must be carefully weighed and mixed. The setting operation often requires heat and pressure. Lengthy set time makes jigs and fixtures necessary for assembly. Rigid process controls are also necessary, because the adhesive properties are dependent on curing parameters and surface preparations. The inspection of finished joints for quality control is very difficult. This also necessitates strict control over the entire bonding process to ensure uniform quality. Non-destructive test techniques cannot quantitatively predict joint strength.
Viscosity measurements in Testing
Testing is an extremely critical function in the adhesive and sealant industry for several reasons. One cannot reliably predict the characteristics of the joint based solely on parameters of the adhesive, substrate, and joint design. Adhesive viscosity is an indication of how easily the product can be pumped or spread onto a surface. It reveals information, together with the liquid’s setting rate and surface tension, that is pertinent to the wetting characteristics of the adhesive and information regarding the age and compounding of the adhesive. Viscosity measurements for free-flowing adhesives or sealants are usually based on one of the following methods described in ASTM D 1084. Adhesive and sealant tests are conducted for a variety of reasons. They are used to either:
There are two general categories of tests for adhesives and sealants: fundamental property tests and end-use tests. Fundamental property tests, such as viscosity testing, are usually employed to assess the consistency of the incoming adhesive or substrate once the joint system is verified as suitable in a specific application. Often fundamental property testing is undertaken after there is a failure or unexplained occurrence to determine if a change in the incoming material may have been the possible culprit. A number of standard tests for adhesives and sealants have been specified by the American Society for Testing and Materials (ASTM) and other professional organizations such as the U.S. Department of Defence and the Society of Automotive Engineers.
Quality control of the incoming materials: It may also be necessary to test the incoming bulk product in-house for fundamental properties. These inspections usually consist of an evaluation of physical and chemical properties such as: color, viscosity, percent solids, weight per gallon, pot life, open time, and flow. An extremely high percentage of defects can be traced to poor workmanship or lack of understanding regarding adhesion. Specifications are a necessary part of a quality control program. A specification simply is a statement of the requirements that the adhesive, sealant, or process must meet in order to be accepted for use.
Adhesives can be single component, but they often consist of two components, the resin and the hardener. All components separately and the mixed product need to be viscosity tested. Some of the standard tests for characterising fundamental material properties for adhesives and sealants are as follows:
Viscosity management in delivery systems
When used for both automotive and general manufacturing purposes, these new industrial adhesives are applied using a wide variety of adhesive delivery systems. These range from fully robotic application systems – which rapidly apply a precise, consistently measured bead of adhesive to a workpiece, such as an unprimed body panel or windshield – to gun-based applicator systems used by plant workers to manually apply adhesives to panels and parts during production line assembly. To achieve a more consistent flow and bead of material during application, fluid viscosity regulators can be added downstream of the pump.
Rheology and viscosity are some of the most important characteristics associated with sealants and adhesives which should display liquid-like properties (they should flow) in order to be applied but must also have sufficient ‘tack’ to stick to or bind substrates together – behaviour which is influenced by viscoelastic properties. Once applied, most materials are then designed to undergo a liquid-solid transition in order form a robust seal or adhesive bond. For low-viscosity adhesives, viscosity is important for penetrating the gluing surfaces and for flowing into the gluing gap. For high-viscosity adhesives the correct viscosity is required to bridge larger gaps and to prevent it from flowing into small gaps and pores on the surface.
Viscosity is a measurement of the flow characteristics and its control is one of the most important operations of the adhesives and sealant delivery steps. Key points on how slurry viscosity is critical:
In order to have a uniform application process and so as not to waste materials and optimise energy usage, it is highly desirable that the viscosity be regulated automatically to a substantially constant value. Real-time, in-line viscosity monitoring and control is essential to improve performance and reduce costs in almost every formulation and delivery process of adhesives and sealants. Process operators realise the need of a viscometer that monitors viscosity and temperature, and could use temperature-compensated viscosity as the key process variable to ensure consistency and reduce failures.
Why viscosity monitoring & control is critical in adhesives and sealants formulations, testing and delivery?
The broad and significant benefits with viscosity management in preparation, testing and application of adhesives & sealants:
To ensure consistent high-quality, defects-free application of adhesives and sealants, the change in viscosity through-out the process stream is monitored in real time, making measurements from a baseline rather than simply measuring absolute values, and making viscosity adjustments by adjusting mixture components and compensating for temperature to keep the processes within specified limits. With continuous online viscosity monitoring, the preparation and delivery can be controlled more effectively, therefore significantly improving the metallurgical properties of the final product.
Process Challenges
Operators in adhesives & sealants market recognize the need to monitor viscosity but making that measurement outside laboratory has challenged process engineers and quality departments over the years. Existing laboratory viscometers are of little value in process environments because viscosity is directly affected by temperature, shear rate and other variables that are very different off-line from what they are in-line. Conventional methods of controlling viscosity of formulations have proven inadequate even in applications where wide variation in viscosity is permitted.
Traditionally, operators have measured the viscosity of slurry using the Zahn flow cup. The measurement is reported as the time elapsed for the cup volume to flow through a hole in the bottom of the cup. The end point of the test must be chosen so that it is consistent from test to test. The procedure is messy and time-consuming. It is inaccurate, inconsistent and non-repeatable even with an experienced operator. In the continuous casting process, the interval sampling causes excessive delays. The viscosity of can’t be adjusted in real time. Besides, the various containers containing the formulation are open; due to changes in ambient temperature, humidity and other factors, such as temperature, dry climate, solvents are likely to be volatile, so cup-based viscosity measurement technique becomes ineffective.
Some companies use thermal management systems to keep point-of-application at a determined optimal temperature to achieve constant ink viscosity. But, temperature is not the only factor affecting viscosity. Shear rate, flow conditions, pressure and other variables can affect viscosity changes as well. Temperature controlled systems also have long installation times and a large footprint.
Conventional vibrational viscometers are unbalanced, requiring large masses to avoid large influence of mounting forces.
Your email address will not be published. Required fields are marked *