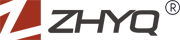
Introduction
An enteric (delayed-release) coating is a barrier applied to oral medication that controls the location in the digestive tract where it is absorbed. The term “enteric” refers to the small intestine; therefore, enteric coatings resist breakdown of medication before it reaches the small intestine. This clever science relies on the fact that the stomach is acidic and the intestines, where food goes after the stomach, are not. Most enteric coatings work by presenting a coated surface which is stable at highly acidic pH found in the stomach, but break down in non-acidic conditions and therefore release the drug in the intestines. Major applications of enteric coatings are pharmaceutical products in the form of solid oral dosage and feed for livestock.
Application
Enteric coating involves application of a film-forming solution onto the surface of an oral dosage form (e.g., capsules, soft gels, tablets, granules, pellets, etc.). The film-forming solution usually contains the acid-resistant polymer, as well as other compounds such as plasticizer(s), colorant(s) or other additives (e.g., anti-adhesive agents, surfactants, flavoring agents, etc.). Pan coating system are traditionally used to apply enteric coatings to oral dosage forms. This method involves spraying the film-forming solution/suspension on the surface of the dosage forms, while the dosage forms are kept in continuous movement in a rotating pan. This technique requires maintaining a controlled balance between spray and evaporation, by applying heated air flow in contact with the surface of the oral dosage form. The process is continued until the desired amount of coating is applied (the desired thickness), and the coating weight gain per unit can be monitored throughout the process. Techniques other than pan coating exist in order to deposit a polymer film on oral dosage forms. These other methods include Wurster coating (air suspension coating) and dip coating. Enteric coating formulations need special care of coating operation due to the constraint of drug release specified in the regulatory requirements.
The functionality of enteric coatings is, for the most part, mediated by a change in pH of the environment to which the enteric-coated product is exposed. Enteric polymers remain unionized (and thus, insoluble) at low pH values, and begin to dissolve at a pH value of approximately 5.0–5.5. In addition, the functionality of enteric coatings can be greatly affected by many factors – one of the primary factors is the coating process:
The choice of the polymer and the thickness of the coated layer are absolutely critical to control the pH solubility profile of the enteric coated dosage form. The result of the coating process is strongly dependent on the rheological characteristics of the film coating dispersion applied. Issues such as logo bridging, orange peel and spray drying are rooted in the viscous and elastic properties of the coating formulation. Determining and appraising the rheological characteristics is therefore of huge importance in order to prevent problems during the film coating process. Film coating quality is absolutely critical and affects the enteric protection and disintegration time of the tablet, and achieving high quality standards is most essential in the pharmaceutical industry.
Moreover, in the field of delayed-release film coating, the process time and, as a result, the manufacturing costs are directly linked to the solid matter content of the dispersion. As viscosity is a specific characteristic of the film forming polymer and the solid content in the solution/dispersion, rheological investigation is very useful and important in order to select the most economical formulation. The increase in viscosity and changes in surface tension influences the droplet formation during spraying as well as film formation, and therefore, the surface quality of the coated cores.
In general, it can be assumed that with lower viscosity:
Each coating formulation and film forming polymer has its characteristic limiting maximum viscosity value for processability which depends on batch size, coating equipment and the process. In order to optimise efficiency and quality, it is absolutely necessary to keep the viscosity optimum throughout the coating process.
The broad and significant factors which make viscosity management critical in enteric coating process are:
To ensure consistent high-quality, uniform coating, the change in viscosity through-out the process stream is monitored in real time, making measurements from a baseline rather than simply measuring absolute values, and making automatic viscosity adjustments by adjusting solvents and temperature to keep it within specified limits.
Your email address will not be published. Required fields are marked *