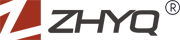
1. Raw water monitoring
1.1. Understand the basic water quality: By measuring the refractive index of raw water, some basic information of raw water can be quickly obtained, such as the approximate concentration of dissolved substances, etc., to help staff preliminarily judge the water quality of raw water and provide basic data for subsequent treatment processes.
1.2. Monitoring pollutants: It can assist in detecting whether there are some pollutants or impurities in raw water that may affect water quality. The presence of certain pollutants may change the refractive index of water. By continuously monitoring the change of refractive index, abnormal fluctuations in raw water quality can be discovered in time and corresponding measures can be taken in advance.
2. Coagulation and sedimentation stage
2.1. Dosage control: The refractometer can monitor the refractive index change of water in real time to reflect the coagulation state of colloidal particles in water. When the amount of coagulant added is appropriate, the colloidal particles in the water will coagulate into larger flocs, and the refractive index of water will show certain change characteristics. Based on the measurement data of the refractometer, the staff can accurately judge the coagulation effect and then adjust the dosage of the coagulant to ensure that the coagulation and sedimentation process achieves the best effect and improves the efficiency of removing suspended matter and colloids in the water.
2.2. Sedimentation effect evaluation: During the sedimentation process, the refractometer continuously monitors the refractive index to help determine whether the sedimentation is sufficient. If the refractive index is stable and within a reasonable range, it means that the sedimentation effect is good and most of the impurities in the water have been precipitated and removed; if the refractive index fluctuates greatly or deviates from the normal range, it may mean that there is a problem in the sedimentation process and further inspection and adjustment are required.
3. Filtration stage
3.1. Filter material performance monitoring: The refractometer can be used to monitor the refractive index of filtered water to evaluate the filtration effect of the filter material. As the filtration proceeds, if the refractive index gradually increases, it may mean that the filter material has adsorbed a large amount of impurities, the filtration performance has decreased, and backwashing or replacement of the filter material is required.
3.2. Filtration effect control: By real-time monitoring of the refractive index, ensure that the filtered water meets the expected water quality standards. Once the refractive index is abnormal, adjust the filtration process parameters in time, such as filtration speed, filter layer thickness, etc., to ensure the stability and reliability of the filtration process.
4. Disinfection stage
4.1. Disinfectant concentration detection: The refractometer can indirectly reflect the concentration of the disinfectant in the disinfection pool. Disinfectants of different concentrations will cause different changes in the refractive index of water. By monitoring the refractive index, the staff can adjust the amount of disinfectant added in time to ensure that the disinfectant concentration is within the appropriate range, which can effectively kill bacteria and viruses in the water without causing excessive disinfectant residues.
4.2. Disinfection effect evaluation: In the water outlet link after disinfection, the refractometer continuously monitors the refractive index, which can be used as an auxiliary indicator for evaluating the disinfection effect. A stable and satisfactory refractive index indicates to a certain extent that the disinfection process is effective and the microorganisms in the water are effectively controlled.
5. Factory water quality monitoring
5.1. Comprehensive quality inspection: The refractometer conducts the final refractive index test on the factory water, which can comprehensively reflect the overall situation of various dissolved substances, impurities, etc. in drinking water. Ensuring that the refractive index of factory water meets relevant standards is an important part of ensuring the quality and safety of drinking water.
5.2. Real-time feedback and adjustment: The online process refractometer can provide data in real time. Once the refractive index of factory water is found to be abnormal, it can be quickly fed back to the staff so that timely measures can be taken to adjust it, avoid unqualified drinking water from entering the pipeline network, and ensure the safety of residents’ water use.
Your email address will not be published. Required fields are marked *