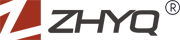
Introduction:
Over the last few years, the ceramic tile industry has undergone significant changes. For these materials, the manufacturing processes are highly innovative, with a fully automated manufacturing process that yields high quality and productivity.
Ceramic tile manufacturers experience a common defect in their manufacturing process that adversely affects the quality of their end product, namely the lack of colour uniformity between tiles of the same model. According to several studies, this defect is caused two ways: First, by an inconsistency in the nature of the materials used in decoration (body, engobes, glazes, inks, etc.) and, second, by improper processing, principally in the application of engobes and glazes, as well as in the decorating and firing processes.
Application:
Most current bell glaze feed systems utilize a metallic pipe inside which the glaze is fed using a pumping system through the top, reaching a constant height through an overflow system. The overflow system may come in different forms depending on the manufacturer. A truncated cone mouthpiece at the bottom of this pipe is fitted with a valve that allows manual control of how much glaze go on to the bell, thus adjusting the amount of glaze applied to the tiles. In the immediate vicinity of the valve there is a straight pipe section, whose diameter matches the outlet diameter of the valve, and at the other end of that pipe is a nozzle with a constant diameter, through which the glaze suspension flows onto the bell.
Viscosity in glazing operations:
It is typically understood in ceramics that viscosity refers to the degree of fluidity of a slurry, suspension or dilution (for example, ‘shear’ is used when discussing viscosity, whereas engineers understand viscosity as layers of molecules or particles that exhibit friction against each other). The opposing concept of fluidity is viscosity. Slurries that are viscous do not possess fluidity, and are therefore thick. Viscosity is measured by laboratory instruments called viscometers, which provide the result in a unit called a poise. The higher the poise number, the more viscous the slurry.
Color variations, coating thickness variations, and cracks are all caused by variations in glazing. Monitoring and controlling viscosity reduces defects dramatically. Lack of colour uniformity between tiles is often attributable to variations in the discharge flow rate of conventional glaze feed systems for bell application because of variations in the viscosity of the glaze contained in the stirring and pumping tanks. These variations in viscosity, mainly caused by temperature changes in the glaze, cause important variations in the quantity of glaze applied to ceramic tiles, which can lead to colour differences. As shown below, variation in the glaze’s viscosity produces variations in the discharge flow rate due to variations in the mechanical energy losses it experiences as it passes through the feeder.
Bubbles and pinholes
During and after firing, bubbles are always present in a glaze. Nonetheless, if the bubbles are too large and not cured during firing, they will appear as defects on the glaze surface.
Conversely, pinholes are caused by gases from the body, which form larger holes when the glaze is not liquid enough to “heal”.
A suitable enrobe layer thickness can reduce the size of the bubbles that travel through the glaze layer. Then adjusting the molten glaze viscosity can help in one of the two following ways:
Dimples
The orange-peel defect occurs when bubbles cannot escape from a glaze due to high surface tension and viscosity and remain beneath the glaze surface. Cooling will cause the bubbles to shrink, leaving a depression on the glaze surface.
Waviness
A glaze surface with waves is usually caused by high viscosity of the molten glaze, which is unable to expand during firing. Usually, the first solution is to increase the temperature or the soaking time in the kiln, but kaolin is also important. The finer the kaolin, the better the surface smoothness.
Current viscosity control methods
The control method used to correct the variations in the glaze flow rate consists of making regular manual measurements (every half hour, in the best of cases) of the grammage applied on to a metallic control plate that is made to cross the glaze curtain created by the bell, so that when the measured glaze quantity departs from the pre-set values, the operator will adjust the valve to increase or decrease the glaze flow rate.
This way of working, given its periodicity, fails to assure application of a consistent quantity of glaze, and leads to defects associated with lack of colour uniformity in the end product.
Your email address will not be published. Required fields are marked *