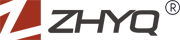
In the extrusion production process, some product quality standards (such as dimensional accuracy or surface flatness of final productsn etc.) require optimal control of the extrusion pressure. The high-temperature melt pressure transducers are of great convern to fulfill these requirements. It will help the production lline more stable and less waste of raw materials when the high-temperature melt pressure transducers and pressure control device are installed at the junction of the mold inlet. Melt pressure transducers play an important role in improving melt quality, improving production safety, protecting production equipment and extending its service life.
In addition, measuring the pressure through the filter screen and the melt pump is also very important for ensuring the safety of production and optimizing the performance of the equipment. If the melt is blocked when flowing into the mold, the sensor downstream of the filter will give an alarm to alert the operator. When the sensor before the filter screen sends an alarm, it indicates that the internal pressure of the extruder is too high, which may cause excessive wear on the screw. For manufacturers using melt pumps, it is necessary to measure the inlet pressure and outlet pressure of the melt to ensure that the melt can continuously flow into the mold, because any obstruction may cause damage to the melt pump.
The common measurement for high temperature pressure measurement is to use capillary to reduce the temperature. Such as pressure measurement of high temperature steam or pressure measurement of high temperature oil. This way is not suitable for high-temperature melt media, because the high-temperature melt will become solid in the capillary due to the decreased temperature and then cannot transmit pressure. Therefore, the pressure measurement of high temperature melt must be direct pressure measurement. This is a big challenge for melt pressure transducers. The temperature of the high temperature melt can reach 300 degrees, 400 degrees or even higher, and the material of the wetted part needs special treatment. The key is that the liquid used to transmit the pressure after the diaphragm requires special material. The filling oil of ordinary diaphragm pressure transmitters is completely unable to adapt to such high temperatures. The Gefran melt pressure transducer M series is filled with high-purity mercury, and uses a special filling process to reduce the interference of impurities and air to achieve good stability. It can accurately transmit the pressure at different temperatures to achieve good linearity of pressure measurement.
Your email address will not be published. Required fields are marked *