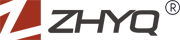
Sensors are widely used in various industries, meeting various needs such as equipment production, building monitoring, media detection, and operation monitoring. They are core industrial products for data production. Accidents caused by bolts loosening and falling off are not uncommon:
At 16:45 on June 29, 2010, the capsule of the “Space Trek” entertainment facility in OCT, eastern Shenzhen, collapsed, killing 6 people and injuring 10 people. The cause of the accident was a loose bolt.
On December 14, 2010, the escalator No. 5 at Guomao Station on Shenzhen Metro Line 1 suddenly reversed from upward, injuring 25 passengers. The cause of the accident was that the fixing bolts of the escalator main unit were loose, and one of them was cut off, causing the main unit support to shift and the drive chain to separate from the sprocket. Under the action of the weight of passengers, the ascending escalator slid down.
In 2021, the US ferry “Wenatchee” suffered a serious main engine failure after an overhaul, and the US National Transportation Safety Board (NTSB) issued a report. One by one, the tightened bolts suddenly loosened, and a connecting rod and half of the piston on the main engine were thrown out of the access hole, causing a fire. The reason for the loose bolts is due to insufficient torque during the overhaul, which causes the piston bushings to fail to align with the crankshaft and lose lubrication, which leads to overheating and bearing failure. Under the extreme force, the connecting rod loosened and ejected through the access port, spewing gas from the crankcase and causing a fire that caused $3.8 million in damage.
In April 2023, a safety accident caused by a falling cylinder bolt occurred in a machinery processing plant. When the worker was operating the press, he suddenly heard a loud noise, and then found that the oil cylinder suddenly stopped during movement and the machine could not operate normally. After inspection, it was found that a bolt on the oil cylinder had fallen off, causing the oil cylinder and the machine to lose support. Although there were no casualties, the damage was heavy.
With the frequent exposure of various safety accidents, the demand for safety monitoring in various facilities is increasing and getting higher and higher, and sensors certainly play an important role in this. However, many safety monitoring and PHM (Prognostics & Health Mangement fault prediction and health management) focus on electrical, gas, important structures and other devices, often the underlying facilities or structural components are ignored. In fact, the more basic the structural safety, the more important it is. The so-called “thousands of miles away” “The embankment was destroyed by an ant nest” is like a bolt, which is the core fastener of all structural parts. Its detection and monitoring require more targeted solutions.
Bolts are mechanical parts that use the object’s inclined circular rotation and friction to tighten objects step by step. Therefore, whether the bolts are tightened or not depends largely on whether they mesh closely with the threaded area of the fixed object, but this close “relationship” is still Will break up. Whether it is bolts, nuts, or fixed materials, the surfaces are mostly hard and will not accommodate each other. The working state of machinery is mostly repetitive movements, and some movements are accompanied by severe vibration and impact. Under frequent vibrations, the originally tightly meshed threads will produce tiny gaps or even deformation. When accumulated to a certain extent, subtle displacement and spin will cause loosening over time.
The traditional method is to use a torque wrench to measure the pretightening force or tension of the bolts, and test them one by one manually. However, since there are often a large number of bolts, simply using manual testing is very cumbersome and laborious, and it is easy to miss. The use of ultrasonic testing not only requires polishing the raised characters on the surface of the bolt, but also requires applying couplant, which makes daily operations more cumbersome.
The “intelligent axial force detection and early warning system” is a new generation of bolt detection and monitoring system. The detection device is directly installed on the top of the bolt. It uses a high-precision internal device to directly measure the micro-displacement of the bolt with an accuracy of 3 μm. No need to polish the bolt or other components. Means, all-weather monitoring, wireless or wired data transmission, convenient and accurate. The unattended design is particularly suitable for locations with harsh environments and inaccessible places without the use of equipment, and plays a very good monitoring coverage function. With three-dimensional dynamic model or digital twin technology, the bolt status of all structures can be grasped at any time and at any place, which plays an important reference role for safety inspection, risk prediction, event traceability and other needs.
In addition to detecting the tightening force, tension, torque, stress, deformation and other parameters of bolts to ensure the safety and reliability of bolt connections, its application fields are very wide, including:
Structural engineering: In the fields of construction, bridges, tower cranes, steel structures, etc., it can be used to monitor the tension of fastening bolts to ensure the stability and safety of the structure.
Automobile manufacturing: In the automobile manufacturing industry, the tightening status of bolts such as engine components, suspension systems, braking systems, etc. can be detected online to ensure the safety and performance of the car.
Aerospace: In aircraft, rocket and satellite manufacturing, it can be used to monitor the tightening status of key bolts to ensure the safety and reliability of the aircraft.
Energy field: used in wind and solar power generation equipment to monitor the bolt connection status of wind turbines and solar panels, and monitor the stability of the wind cylinder to improve the efficiency and life of the equipment.
Railways and rail transportation: In trains and subway systems, used to monitor the tightening status of track bolts to ensure the safety and operation of trains.
Manufacturing: In manufacturing, it can be used in automated assembly lines to monitor the status of bolt connections in moving devices to ensure product quality and consistency.
Pressure vessels and pipelines: In chemical engineering and petroleum industries, it can be used to monitor the bolt tightening status of pressure vessels and pipelines to ensure safe operation.
It is used in a wide range of engineering and manufacturing applications where the safety, reliability and performance of bolted joints need to be ensured. By monitoring the status of bolts in real time, problems such as loosening, breaking or over-tightening of bolts can be prevented, thereby improving the safety and maintainability of equipment and structures. Risk judgments can also be made based on the trend of slight changes.
In general, “Risk warning not only requires knowledge in mathematics, computer science, operations research, physics, chemistry, materials science, engineering and other aspects, but on-site micro-deformation monitoring is also a very important parameter. Intelligent axial force detection and early warning “System” is an important part of daily monitoring and PHM systems, ensuring safety today and in the future.
Your email address will not be published. Required fields are marked *
PT124B-502 high precision stainless steel explosion-proof flange liquid oil diesel fuel turbine flow meter
2023-04-28